Matec Filter Press Operations
Zinkan has been working hard in conjunction with Matec to further streamline the process and ensure that only critical personnel are required to operate the system. Most often the responsibility of the equipment is a side job of one individual. This is largely due in part to the automation and remote access ours systems offer. Equipment can be a lot to manage as an operator or owner; there is maintenance, breakdowns and general labor concerns when trying to run a plant.
Matec has designed almost all of these headaches out of their equipment and the result is truly impressive. This Water Facts details all the unique attributes of our Filter Press Operation that make it stand apart from the competition.
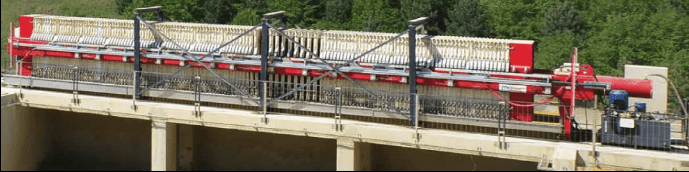
What makes a Matec Press Unique?
An ancient technology serving the future. Filter presses are based on a simple, ancient principle, invented by the Romans to press olives and grapes. Today’s technology brings the Matec filter press back to the present as a modern, invaluable tool. Simplicity, flexibility and effectiveness make it essential for many industries. Matec’s philosophy focuses on the relentless search for harmony between the productivity requirements of a modern company and safeguarding the environment. The filter press dehydrates the sludge by squeezing all the water out of it (recovering about 90% of it) into dry cakes of pressed sludge, which can be handled, moved and are ready to be reused or disposed of — all in a seamless integrated and automated package.
Automatic Real Washing:
The filter press can be equipped with an automatic washing system for plates and cloths. The system is composed by one valve, one system of pipes on the mud head side of the filter press, and discharging valves on every single plate. The feeding pump sends clean water to wash the residual mud. The system washes the plates 20 by 20. The frequency of the washing cycle is set through the operator panel.
Mud Cake Washing:
Special mud with chemicals may require the washing of the cakes with clean water to lower chemicals’ level below the required threshold. The clean water is pumped inside the chambers before the discharging. A membrane squeezing is usually required for this accessory.
Membrane Squeezing:
When cakes with a very low residual moisture are needed, Matec filter press can be equipped with membrane plates. Water is pumped into the special plates which grow in volume to squeeze the cake and lower the moisture.
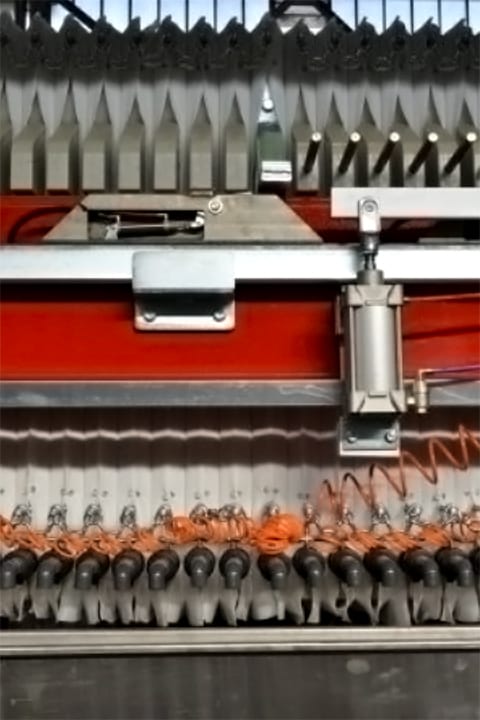
Other Value Added Components of a Matec Filter Press:
Core Blow:
The core blow system is a system conceived to clean out the residual liquid mud which remains in the diffusion conduit which goes through the plates. It is done when the filtration cycle has ended, but before the cake discharging. The filter press is equipped with a compressed air system that pump air from the mobile plate to remove the residual liquid mud from the plates. The blown mud is discharged into the mud homogenizer tank again or into the waste water pit.
Cake Dryer:
The cake dryer system is installed to lower the residual moisture of the cakes by injecting air into the filter press. The air dries the cakes and is discharged through the drainage system.
Drip Tray:
The Drip Tray System is a system conceived to prevent the dripping of water on the already discharged mud cakes. It works automatically, controlled by the PLC and moved by a dedicated motor / gearbox system. The tray is placed under the filter press during the filtration cycle and it shifts away when the filter press opens for the cakes’ discharging.
Plates:
The plates are the meat of the filter press. These components are what enable the shaping of sludge cakes by forming a seal with closed pressure. Specifically sized mesh covers are placed over the plates which allows for the filter process to occur when sludge is umped through them at high pressure thanks to Matec’s HPT, High Pressure Technology, pumps.
Fixed Head:
The fixed head is the plate at the inlet of the sludge feed. This plate does not move at all as it is the base for the rest of the plates. This is the plate that can make or break the pressure tight seal for the rest of the unit which is why it is important that it cannot be moved.
Movable Head:
All of the plates following the fixed plate are technically movable plates. The end plate, farthest from the inlet feed, is most notably a movable plate because it will be the first removed if needed. Plates extend once a cycle is completed to drop the sludge cakes and then contract to the starting position in preparation for another cycle to begin.
Control Box:
The control box is typically located at the end of the filter press that is farthest from the inlet sludge feed. This is the brain of the filter press. There is a touchpad that has a series of commands for the filter press to follow. There are also knobs that can adjust the settings of the filter press to “off,” “manual,” and the most noticeable feature, “automatic.”
HPT Pump:
The pump used to feed sludge into the filter press is a High Pressure Technology Pump, or HPT Pump for short. HPT pumps has a pressure range from 16 to 21 Bar which will force sludge from the bottom of the clarifier into the filter press which enables the plates to filter the material.
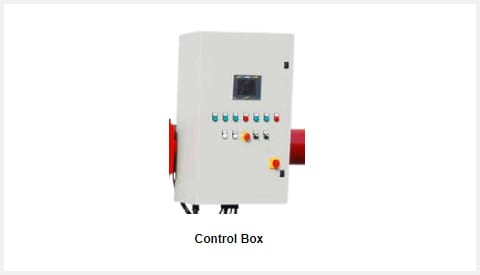
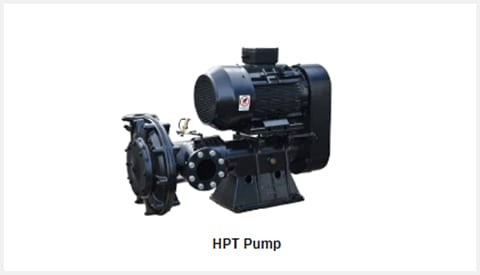
About The Author
Nick Piskura is the Marketing and Web Development Specialist at ChemREADY who utilizes expertise in digital marketing strategies to provide knowledgeable insights in each segment of our business. Nick provides insights through web development and multimedia resources that support ChemREADY’s full range of services, including Legionella management, ANSI/AAMI ST108 compliance, boiler and cooling tower treatment, wastewater processing, and industrial water quality solutions.